- Home
- Société
- Garlock Regional Websites
- Garlock Europe
- PS-SEAL Lip Material Test
PS-SEAL Lip Material Test

Welcome to the Garlock Europe Blog / Garlock Europe Knowledge Hub.
Here we would like to keep you up to date with the latest news from Garlock Europe. Learn more about research, development, products, technologies, news and trends. We are happy to answer your questions about the European market and our solutions.
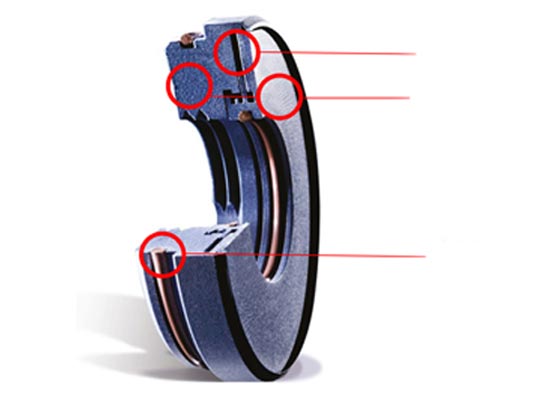
How to avoid bearing damage in rotating applications that require the use of aggressive chemicals.
Moisture, dust, and dirt are just a few examples of contaminants that can enter a bearing housing. Contamination causes a number of problems including seal degradation. The result: leakage, which poses a significant safety risk to employees and the environment. Labyrinth seals provide a remedy here. They are low-wear and reliable in use.
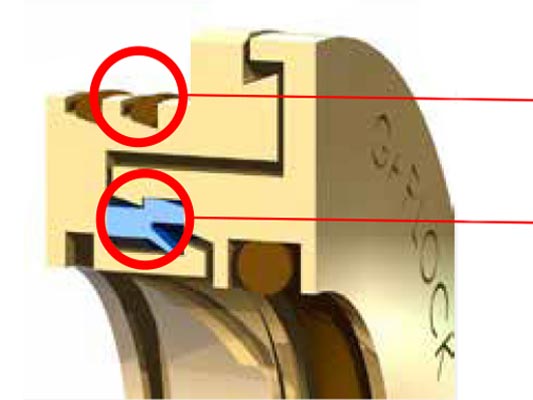
Permanently avoid bearing damage due to liquid ingress and contamination in pumps, motors and gearboxes!
Lubricant contamination often leads to bearing damage in pumps, motors and gearboxes. A large proportion of contamination enters the bearing housings through gaps and openings. This occurs primarily at the points where shafts go through the bearing housings or at vent openings. In addition, temperature fluctuations during daytime and nighttime hours, as well as during operating and rest periods, cause vapours to expand and contract.
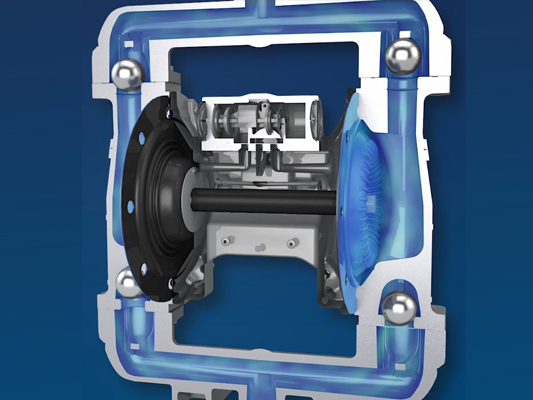
Diaphragms in pneumatically & hydraulically operated diaphragm pumps
Diaphragms are used in numerous applications, including valves, fittings and actuators. Their use in air-operated diaphragm pumps and hydraulically operated diaphragm pumps is very widespread due to their versatility.
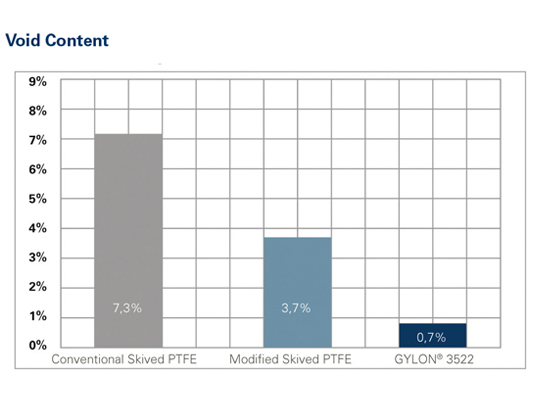
Reduced void content and increased flex life with Garlock Diaphragms
The GYLON® Style 3522 PTFE diaphragm is characterized by outstanding properties. Two of these are the reduced void content and the increased flexibility.
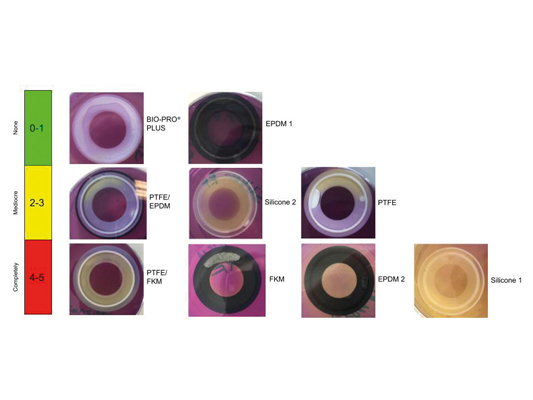
Hygiene is a question of attitude. Or is that different for your plant?
The pharmaceutical and food processing industries are urgently interested in limiting and avoiding all downtime caused by cleaning and maintenance procedures. Sterilization cycles are performed in the tightest possible time, with highly concentrated chemicals, high temperatures and increased flow rates.
So this attitude towards hygiene is right.
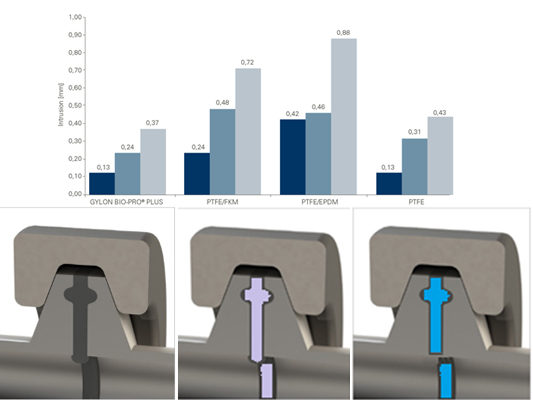
Contamination through seals! A horror for operators of any plant. But how to get a grip on it?
The high hygienic requirements in industry rightly demand cleaning processes that must be ever cleaner and faster.
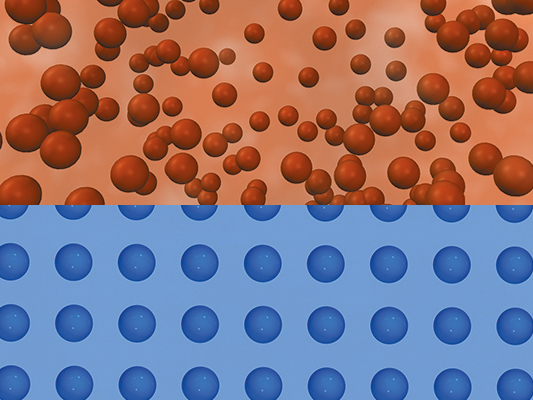
GYLON® production process – a comparison to the conventional PTFE gasketing production process shows the difference.
PTFE – PolyTetraFluoroEthylene - is an unbranched, linear, semi-crystalline polymer of fluorine and carbon. Due to its chemical inertness, PTFE is used as a coating where aggressive chemicals occur in industry.
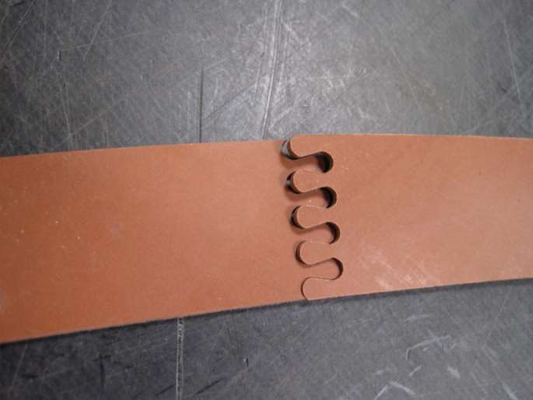
The Welded GYLON® Process – for large gaskets without handling problems or premature blowout.
GYLON® is a high performance PTFE (Polytetrafluoroethylene) gasketing material with excellent chemical resistance in combination with stopped cold flow based on the special GYLON® production process. GYLON® was introduced by Garlock in 1967. From then on it was further developed by Garlock according to the requirements of the different industries, their processes and the media involved.
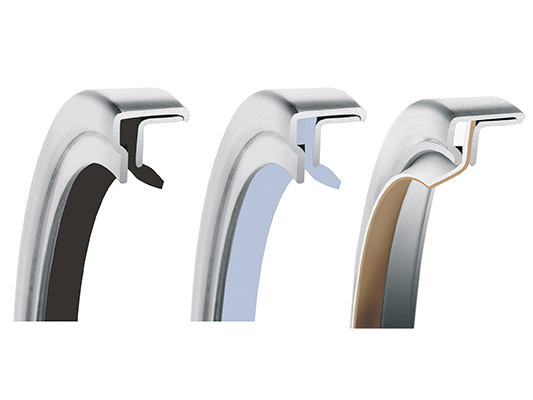
PS-SEAL® Non-Standard – dynamic seals in standard sizes with different lip materials
The Garlock PS-SEAL® Standard with a GYLON® Black lip and the static seal made of FKM has long been known in industry as a proven sealing element in critical sealing situations.
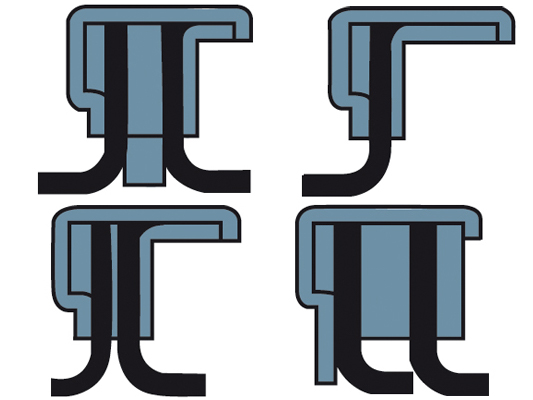
PS-SEAL® Non-Standard - dynamic seals in standard sizes with different lip configurations
The Garlock PS-SEAL® Standard is a PTFE-based high-performance seal that meets a wide range of requirements in practical use.
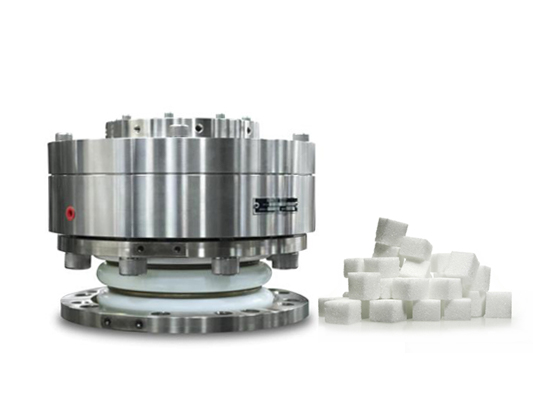
Swing in the sugar crystallizer
Sugar production is a rather moving business. To crystallize the sugar, the syrup is heated to evaporate the water content. This process is best carried out in a vacuum, as lower process temperatures are possible and the risk of discoloration (burning) of the sugar crystals is considerably reduced. During crystallization a viscous slurry is produced. Agitators keep this slurry in motion so that the sugar crystals can grow.