- Home
- Recursos
- Capacitación
- Product Selection
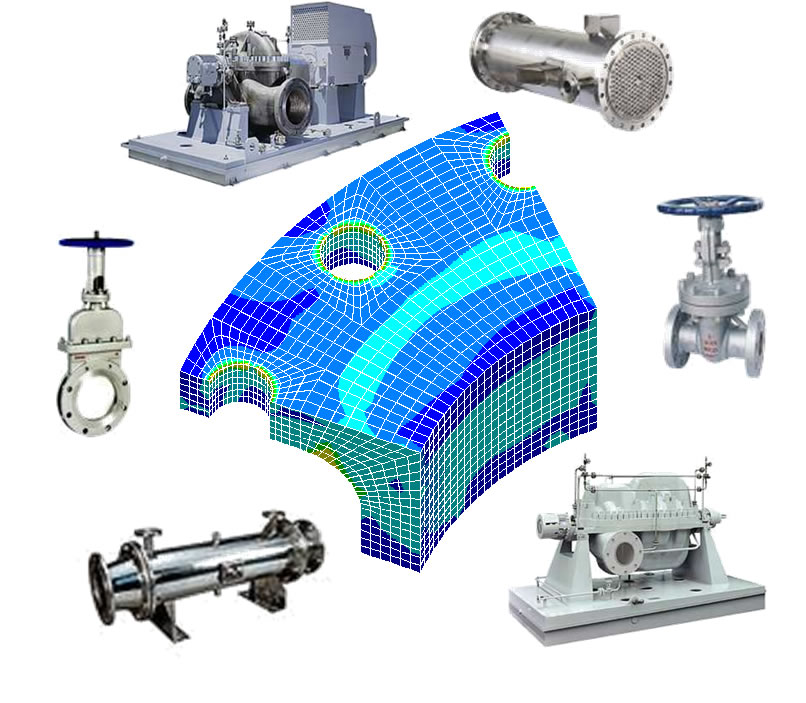
Product Selection
Forces Acting on Sealing Devices
Before we can properly select a sealing device, it’s important to understand the forces acting on the sealing device in the application. First, we will look at the forces in a flange assembly where a gasket is used.
Forces Acting on a Gasket
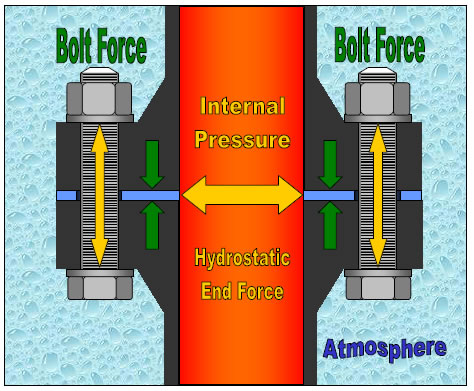
In a flange assembly, the gasket is placed between two flanges, which are then clamped together with bolts, studs, or other clamping devices.
In this example, the bolts are creating a clamping load, or bolt force, which compresses the gasket.
Once the media is introduced in the system, the internal pressure that is generated will try to push the gasket and separate the flanges. This force is called hydrostatic end force. If the hydrostatic end force exceeds the bolt force, the flanges will separate, and the gasket will leak or blow out.
The last external force we have to consider is the atmosphere. In other words, what’s going on outside the flange assembly?
In a packing or hydraulic application, compressive load is applied to the sealing components by a cylindrical device called a gland.
This compressive load causes the sealing components to expand radially, which then creates a seal between the wall of the stuffing box and the shaft, stem, rod, or ram.
When the media is introduced, it can also create additional radial expansion by way of hydrostatic load, as it tries to push the sealing components out of the stuffing box.
Lastly, shaft movement needs to be taken into consideration. How the shaft moves (rotary or reciprocating) and at what speed will directly impact the sealing device selection process.
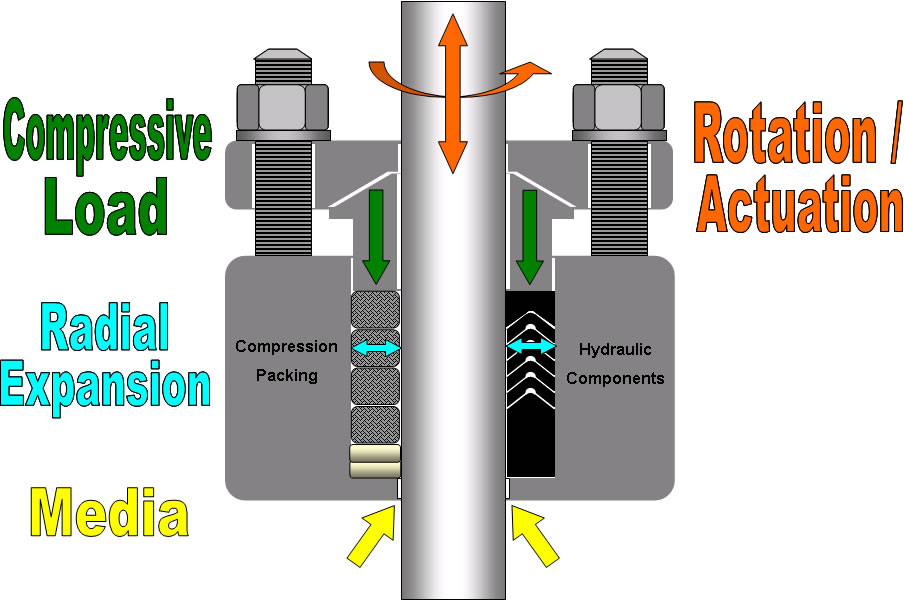
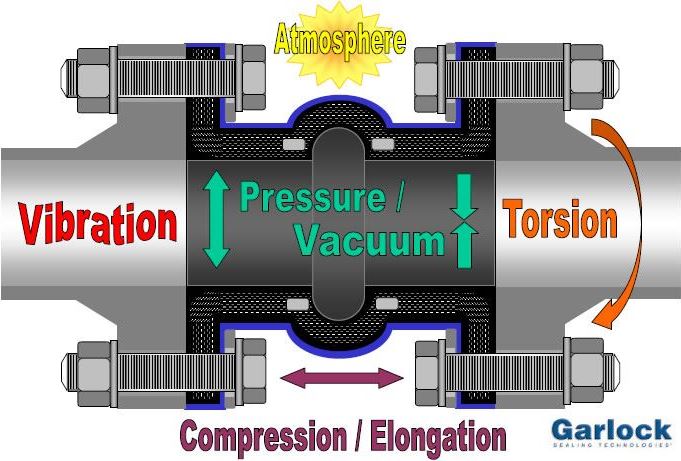
Some flange assemblies require an expansion joint, which may be used to counteract or minimize unwanted dynamic forces in the system.
These forces can be in the form of vibration, twisting or torsional movement, compression, and elongation. In addition, the expansion joint must be able to hold up to system pressure, positive or negative (vacuum).
Lastly, the exterior of the expansion joint has to be designed to withstand external atmospheric conditions, such as oil, water, and ultra-violet ray exposure.
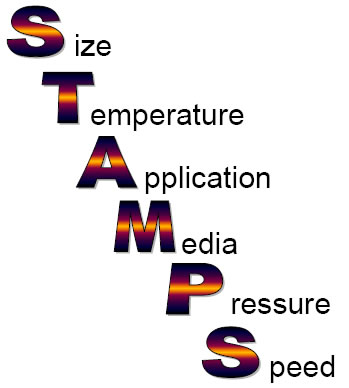
Product Selection Criteria (STAMPS)
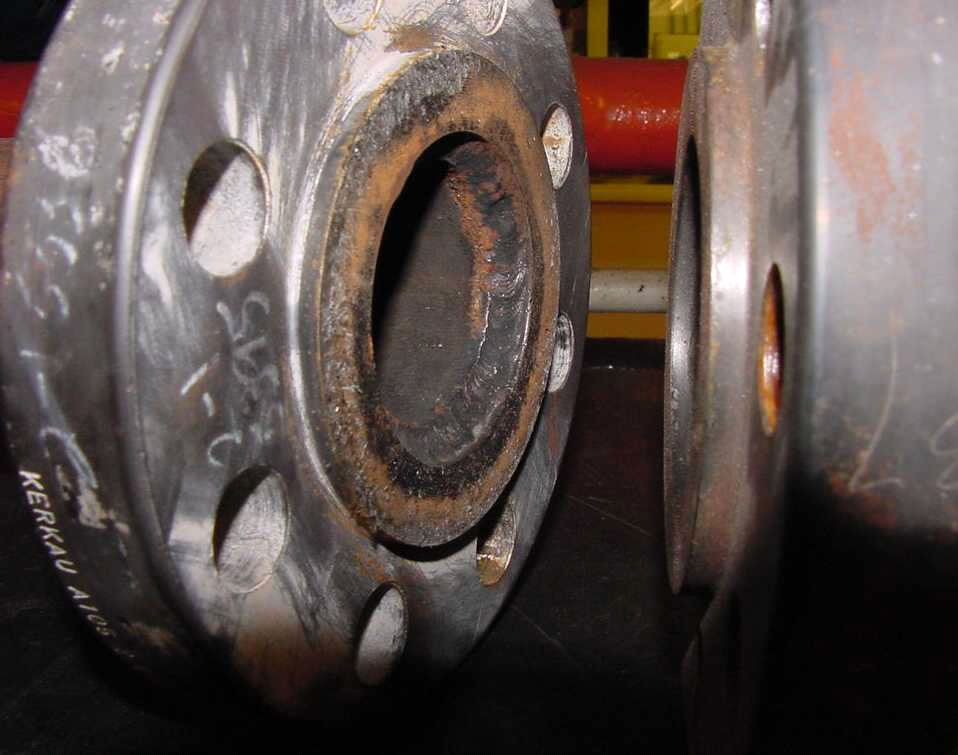
Gasketing
Gaskets are most often used in connections called flanges. While there are industry-standard sizes and classes, such as 3”-150#, non-standard flanges can also be found throughout a plant.
When dealing with a non-standard flange, it is very important to obtain as much detail as possible about the contact dimensions (the portion of the gasket actually being compressed) and the fasteners or bolts (size, grade, quantity).
The Applications Engineers at Garlock can then use this information to calculate the contact area and available assembly stress. This is a key factor in the selection process, as an improperly loaded gasket could result in premature equipment failure.
Compression Packing and Hydraulic Components
Compression packing and hydraulic components are commonly placed in a chamber of a pump, valve, or cylinder called a “stuffing box”. The dimensions of the stuffing box will directly impact the cross-section of material required for the application as well as the number of rings. In addition to rings, bushings may be used to take up additional space in the stuffing box that may not be required for the sealing product being specified.
For additional information on how to calculate packing cross-section, recommended shaft finish, and recommended number of rings per application, please refer to the compression packing or hydraulic components technical guides.
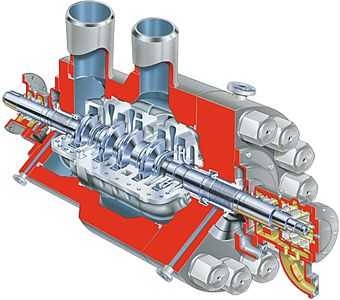
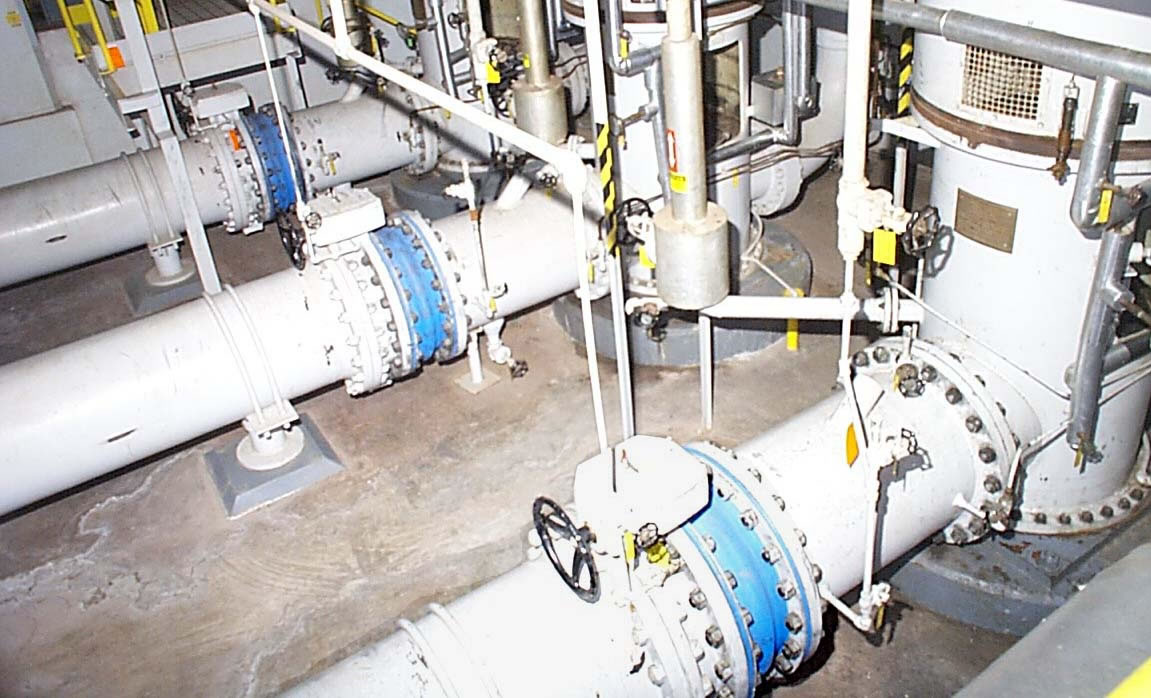
Expansion Joints
Expansion joints, like gaskets, are commonly used in flanged connections and are available in industry-standard sizes and classes. When dealing with non-standard flanges, similar flange and bolting information is necessary in order to properly build the expansion joint.
However, unlike gaskets, expansion joints have an additional dimensional plane that needs to be taken into consideration, called the “face-to-face” dimension. In addition, it is very important to obtain accurate dimensions if an offset and/or misalignment exists between the flanges.
Garlock is one of the few expansion joint manufacturers that custom builds expansion joints to fit an assembly. This not only makes installation easier, but it provides improved service life and movement capability. Knowing how much compression and elongation is required in the assembly is also very important, as that can directly impact the type of arch (abrupt versus self-flushing) and number of arches.
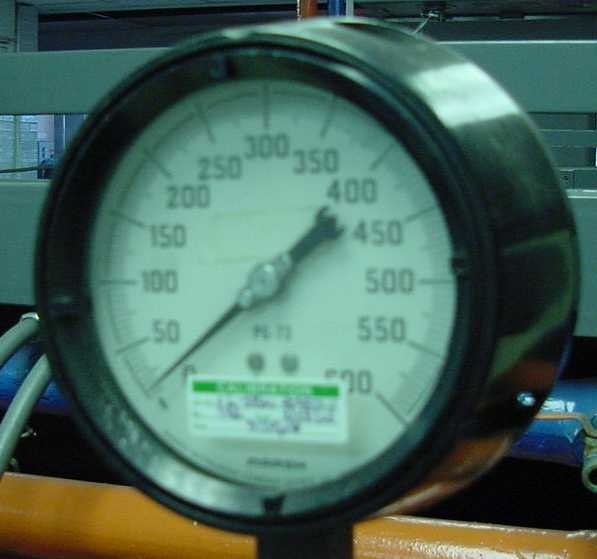
While many systems operate at a continuous temperature, it is important to recognize and take into consideration any system temperature spikes and thermal cycling if they exist.
When the system temperature fluctuates quickly due to spikes or thermal cycling, the sealing device must react to any movement that occurs in the application related to expansion, contraction, and change in internal pressure.
Cryogenic conditions must also be properly handled, as most materials (in this case, sealing devices) have a low-temperature limit where the material becomes brittle. If this occurs, the product may crack or break and result in premature failure.
Application is similar to Size in that it relates to the equipment where the product is being used. However, unlike Size, application data may contain additional details that would not otherwise be uncovered by the basic dimensional or size information.
For example, the size of a stuffing box does not tell you if it is a valve that is actuated by hand every few days, or a pump spinning at 4000 feet per minute, but the packing products that would provide the best performance in each of these applications are completely different.

Bolts & Fasteners
The most common method to clamp sealing devices in place is by using fasteners or bolts. There are multiple variables in a fastener that must be identified and understood in order to ensure that the sealing device receives proper loading.
First, we need to determine if the bolt or fastener threads are fine or coarse threads. Coarse threads, which are by far the most common in industry, are stronger, but not as efficient as fine threads. Therefore, a fine thread bolt requires less torque to generate the same load as a coarse thread bolt.
Secondly, flat washers can greatly improve load translation into the sealing device by creating a bearing-like surface for the nut or bolt head to slide on. Without washers, it is more likely that the nut or bolt head will bind against the contact surface of the flange, valve, or other equipment.
The third variable to consider is thread coating. Coatings are typically applied to improve fastener corrosion resistance. In addition, they can improve efficiency, thus resulting in higher compressive loads at a given torque.
The fourth variable to consider is thread lubricant. A non-lubricated bolt has less than 50% of the efficiency of a lubricated bolt. What that means is if you torque a non-lubricated bolt to 60 ft. lbs., the compressive load it generates will be approximately half of the load you would generate with the same bolt when lubricated. This concept will be demonstrated in the next few sections.
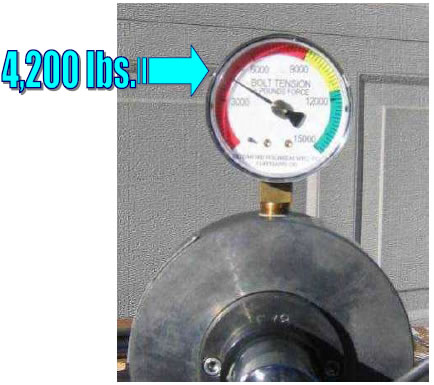
Bolt Force – Bolt #1 – No Lubricant
The device shown is a bolt tension device that is designed to measure load generated in pounds (lbs) when a given torque value is applied. In this example, a 5/8” SAE Grade 5 coarse thread carbon steel bolt has been installed and torqued to 60 ft. lbs. The resulting stress that is generated is 4200lbs.
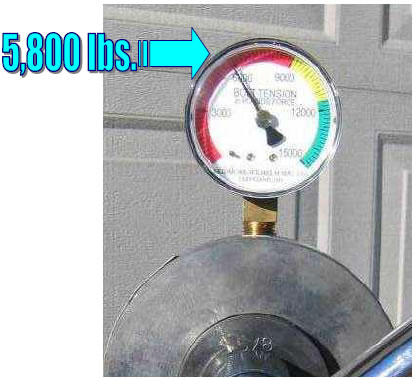
Bolt Force – Bolt #2 – Zinc-Plated, No Lubricant
In this example, we are now using the same size and grade, but this is a zinc-plated bolt. As you can see, in this case, the coating improves the efficiency of the bolt and the load generated. When the same torque of 60 ft. lbs. is applied, the compressive force generated increases to 5800lbs.; nearly a 30% increase in available compressive force.
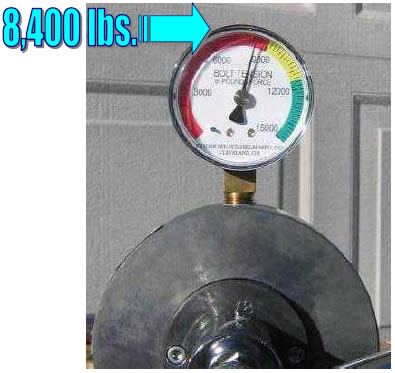
Bolt Force – Bolt #3 – Zinc-plated with Lubricant
The last example is the same size and grade zinc-plated bolt, but with thread lubricant (nickel-based Never Seiz). The compressive load generated with the same initial torque of 60 ft. lbs. is now 8400lbs! That is twice the force generated by the original carbon steel bolt, thus proving the importance of properly lubricating bolts.
Bolt Grade
This chart shows the more common fastener grades used in industrial applications, as well as their yield strengths, which is the stress point at which a bolt becomes permanently deformed (In other words, it will not spring back to its original size when the load is removed).
Bolt grade identification is extremely important when determining proper torque values for an assembly.
For example, ASTM A193 B8 stainless steel bolts are commonly used for chemical services where corrosion resistance is required. Here, there are two different B8 bolt designations shown, however, there is a significant difference in yield strength between a class 1 (most commonly used stainless steel bolt in chemical service) and a class 2 (strain-hardened stainless steel).
Notice the only difference in how these bolts are marked is a single line under the “B8” marking, thus emphasizing the importance of properly reading the markings.
For a more comprehensive list of bolt grades, contact Garlock Applications Engineering.
Media
Media is the fluid the sealing device is sealing in or out of an assembly.
Sealing devices are typically used to seal gases and/or liquids. Occasionally, a sealing device may be required to contain media in a solid form, however, many of these applications are in slurry form (a liquid and solid mixture). When choosing a product to seal a particular media, it is important to consider not only chemical compatibility but also emissions compliance.
For example, a sealing device that works very well for sealing liquids may be chemically compatible with certain gases but may not provide the necessary level of permeation resistance.
When dealing with refining applications, the two most common hydrocarbons encountered are the aliphatic and aromatic. Aromatic hydrocarbons, such as toluene, benzene, and xylene, are more chemically aggressive than aliphatic hydrocarbons, such as petroleum oil, kerosene, and diesel fuel. Therefore, aromatic hydrocarbons usually require more chemically-resistant sealing devices made from PTFE, graphite, or metal, where aliphatic hydrocarbons can be sealed with sealing devices constructed from fiber (I.E. aramid) and elastomers (nitrile or fluoroelastomers).
When dealing with strong oxidizers, alkalines, and acids, it is very important to understand the chemicals involved and their concentrations.
pH Scale
The pH scale is used to measure the hydrogen concentration of a chemical. As you can see from the chart shown, common household products that are used every day can, at the right concentration, have a similar pH rating to hazardous chemicals used throughout industry.
Pressure
Most systems operate at some sort of “constant” pressure, however, if system upsets occur, it is important to factor that into the selection process, as well as make operational corrections to try to prevent those upsets from occurring. Here are a few examples of system pressure upsets:
Surging
Surging is when system pressures are drastically increased over a short period of time. In many cases, these surges are due to valves being opened too quickly or pumps that are “dead headed”.
Hammering
Hammering can actually be created in a system in a few different ways. One of the most common ways hammering is created is when valves are shut too quickly; when fluid travels through a pipe, the product has forward-moving inertia, and the rate at which it moves is called velocity. A system can have high velocity at very low pressure, therefore, if a valve is closed quickly, the system must absorb the inertia of the media. The result can be similar to a car hitting a brick wall; something has to absorb the energy. In most cases, the sealing device is the weakest point in the assembly, and therefore takes the impact. The systems most commonly subjected to sealing device failure due to hammering are steam systems, and the phenomenon is usually a result of process condensate not being properly removed or drained from the system.
Thermal Expansion
Unlike gases, liquids do not compress. Therefore, when a liquid is heated in an enclosed space, with no air space for expansion, the internal pressure that is generated can be catastrophic to the system, equipment, and/or sealing devices in the system. For example, for every 1°F you increase to the temperature of water, it will in turn generate approximately 20-30psig of internal pressure. That means that a 10°F swing in operating temperature could generate 200-300psig of internal pressure if the water was fully contained.
Speed
The last portion of STAMPS is the Speed.
Speed information is required for compression packing and hydraulic components used in pumps and other rotating or reciprocating equipment.
In the case of rotating equipment, the speed must be expressed in feet per minute (FPM). The reason speed is expressed this way is that a large-diameter shaft rotating at a given number of revolutions per minute (RPM) will actually have a higher FPM surface speed than a small-diameter shaft rotating at the same RPM.
In reciprocating applications, it is important to know the length of the stroke and cycles per minute. This information will then be used to calculate the speed of the shaft or piston.
Conclusion and Test
This concludes the Garlock Fluid Sealing Basics: Product Selection course. You may proceed to the testing portion.
Take the Garlock Fluid Sealing Basics: Product Selection Test